Some problems while trying to replace my ball joint
#1
Some problems while trying to replace my ball joint
After reading ball joints 101, and thinking it seemed realitivly easy, so I thought i'd give it a shot on my front passenger side, which is REALLY bad..
I took off the wheel, got the three main bolts off, and then spent the next 6 hours killing myself trying to get the ball joint to sepearte. I even used and opposible pickle fork, but in the end I just had a really loose ball that would roll around any way you wanted, but would not seperate.. Out of frustraion I just grinded the joint off just below the flange.
http://i5.photobucket.com/albums/y15...x/grinding.jpg
http://i5.photobucket.com/albums/y15...fballjoint.jpg
The pickle fork probably accoutned for why its soo lose.. But theres now way that ball joint was gonna sepearte..
However, i'm fearing that grinding the thing off may have been a bad idea because if the top part of the joint is actually threaded into the flange (and not just letting the top spindle nut hold it in place) I'm kind of screwed... *mutters something about puns* (well, my only way to get the bolt out (should it be threaded would be to use the hole thats meant for the spindle clip)
http://i5.photobucket.com/albums/y15...stillstuck.jpg
http://i5.photobucket.com/albums/y15.../boltstuck.jpg
I then realized my second mistake, when i found out my wrench set only went up to 19 mm. I used a lock wrench, but couldnt get the bolt to budge.. And I found it unnerving that the whole wheel assembly moved while i was applying pressure to the nut.
Im gonna go buy a 22mm wrench first thing in the morning, and hope i can get it back in working order so I can get to my afternoon class.
but ya, should the upper balljoint bolt just fall out if I get the 22mm spindle nut off?
Also, where are the tie rod ends on this part.. I know theres the axle, cv joint, then the control arm which bolts to the ball joint.. Reason being.. Have I messed up my allignment while doing this?
I took off the wheel, got the three main bolts off, and then spent the next 6 hours killing myself trying to get the ball joint to sepearte. I even used and opposible pickle fork, but in the end I just had a really loose ball that would roll around any way you wanted, but would not seperate.. Out of frustraion I just grinded the joint off just below the flange.
http://i5.photobucket.com/albums/y15...x/grinding.jpg
http://i5.photobucket.com/albums/y15...fballjoint.jpg
The pickle fork probably accoutned for why its soo lose.. But theres now way that ball joint was gonna sepearte..
However, i'm fearing that grinding the thing off may have been a bad idea because if the top part of the joint is actually threaded into the flange (and not just letting the top spindle nut hold it in place) I'm kind of screwed... *mutters something about puns* (well, my only way to get the bolt out (should it be threaded would be to use the hole thats meant for the spindle clip)
http://i5.photobucket.com/albums/y15...stillstuck.jpg
http://i5.photobucket.com/albums/y15.../boltstuck.jpg
I then realized my second mistake, when i found out my wrench set only went up to 19 mm. I used a lock wrench, but couldnt get the bolt to budge.. And I found it unnerving that the whole wheel assembly moved while i was applying pressure to the nut.
Im gonna go buy a 22mm wrench first thing in the morning, and hope i can get it back in working order so I can get to my afternoon class.
but ya, should the upper balljoint bolt just fall out if I get the 22mm spindle nut off?
Also, where are the tie rod ends on this part.. I know theres the axle, cv joint, then the control arm which bolts to the ball joint.. Reason being.. Have I messed up my allignment while doing this?
#2
Ah yes, the good ol spinning nut while you wrench away 
Next time that happens to me I'm using a Nut breaker, wish I would've known about it back then.
Here, I had the same problem. AND I did the same as you by HAND with a HACKSAW!!!!1one! man that was a PITA!

Next time that happens to me I'm using a Nut breaker, wish I would've known about it back then.
Here, I had the same problem. AND I did the same as you by HAND with a HACKSAW!!!!1one! man that was a PITA!
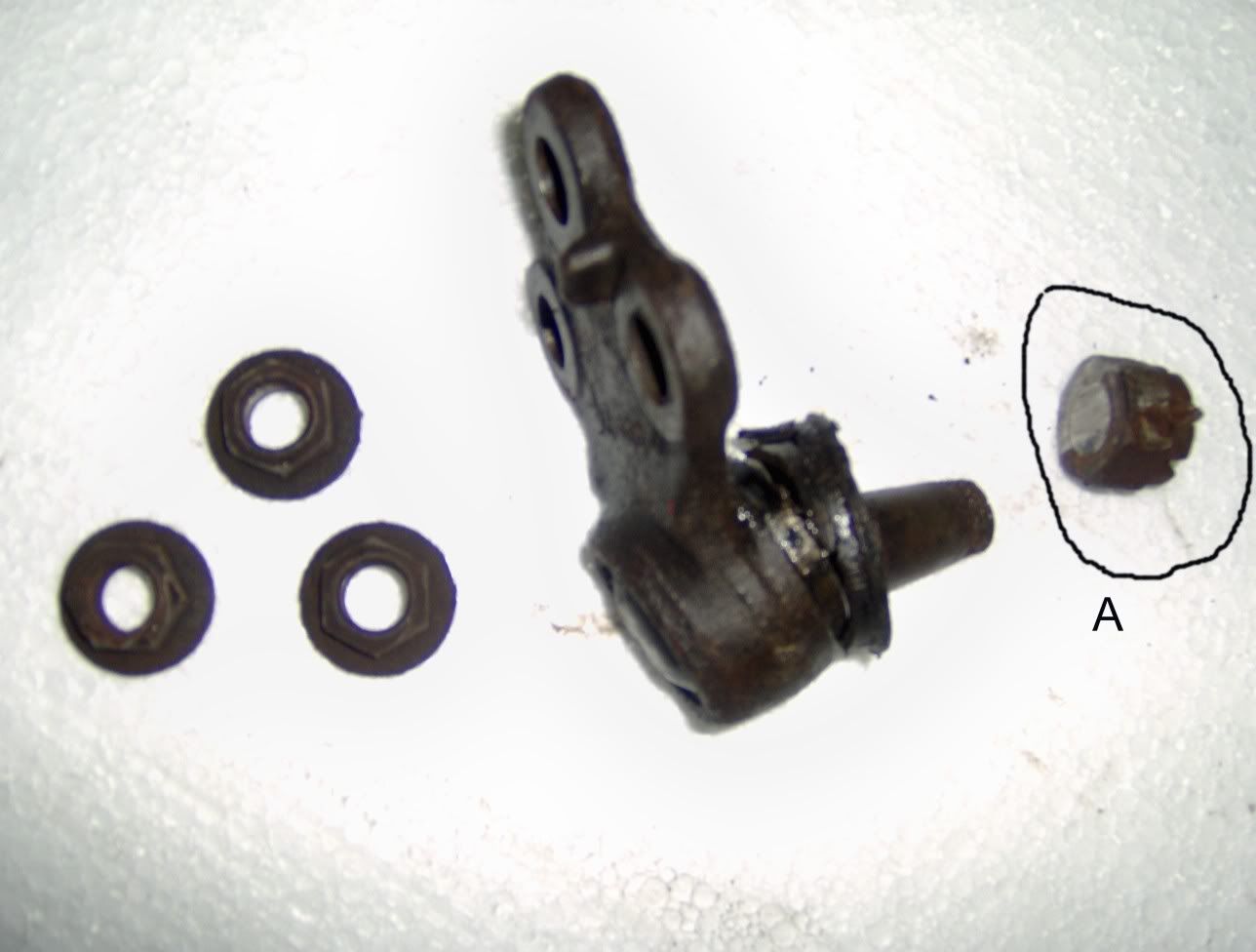
#3
mmk, so should the rest of the upper balljoint fall free if I manage to get the 22mm nut from hell loose (15 yrs of rust) or is it actually threaded into the flange?
Wait a min... what is that that you have circled as A? Is that the spindle nut? hacksawed from the top of the flange? blah I grinded from the bottom... looks like i may be doing some hacksawing myself if the wrench dosent work
Wait a min... what is that that you have circled as A? Is that the spindle nut? hacksawed from the top of the flange? blah I grinded from the bottom... looks like i may be doing some hacksawing myself if the wrench dosent work
Last edited by smitty124; 11-25-2007 at 11:19 PM.
#4
Mine came right off after cutting it. Do you have a torch? If not, you should cuz that is your best friend for suspension work.
have you tried holding the 22mm wrench in place and banging with a hammer from the other end?
have you tried holding the 22mm wrench in place and banging with a hammer from the other end?
#5
yep.. I got a 22mm wrench and used that with a hammer , and successfully converted a 22mm nut, into a 22mm clyindrical washer... WHY DOSENT ANYTHING WORK>!?!?! BLAH
*brings out the dremel and hacksaw*
*brings out the dremel and hacksaw*
#6
- if you removed the upper nut on the ball joint tap it w/ a hammer down and it should fall out. it's not threaded in.
- tie rod is another ball joint looking thing that's on the rear part of the wheel. if you didn't move it your alignment "should" be ok.
at this point you can get the 22m wrench but there's no way you can use the wrench and take off the bolt. it's way to messed up. cut it off...get a hammer and tap the extra slug piece out to the bottom.
that's why i tell people to take the axle off the spindle since you have A LOT more space to work on and it's a straight shot down.
the circled piece in john's pic is the upper nut on the spindle...basically the piece you should cut off.
- tie rod is another ball joint looking thing that's on the rear part of the wheel. if you didn't move it your alignment "should" be ok.
at this point you can get the 22m wrench but there's no way you can use the wrench and take off the bolt. it's way to messed up. cut it off...get a hammer and tap the extra slug piece out to the bottom.
that's why i tell people to take the axle off the spindle since you have A LOT more space to work on and it's a straight shot down.
the circled piece in john's pic is the upper nut on the spindle...basically the piece you should cut off.
#7
They don't usually round off like that when you are whacking the wrench with a hammer, that usually happens when you are using a pipe over the wrench to get extra leverage on it. You can almost always see when a nut / bolt begins to strip, and stop monkeying it in time to save it. When I see one starting to round off on me, I stop, and heat it up with a torch (even propane will do the job most of the time), then when it is good and hot, I spray it down with liquid wrench. The cool lubricant on the hot threads does two things, the oil wicks into the threads, and the quick change in temperature mechanically breaks the threads loose. This almost always works.
Once the bolt / nut is rounded, sometimes you can grind two flat sides on it with a dremel tool, then grab it with a smaller wrench. or vice grips. I haven't had much luck with the nut breakers, but I know people who have. Grinders are usually easier to cut off nuts with than the hack saw is. Finally, Sears makes a set of tools for removing rounded nuts / bolts. They work basically like screw extractors, but they fit over the rounded head instead of going into a drilled hole. I have had some luck with them in the past.
You would have saved yourself a lot of work by dealing with that nut instead of cutting the ball joint apart. You CAN NOT use the pickle fork to remove the joint until that nut has been taken off! Once the nut is off (either by unscrewing it, or by cutting / grinding it) then the pickle fork will pop the joint out with just a few good whacks.
Once the bolt / nut is rounded, sometimes you can grind two flat sides on it with a dremel tool, then grab it with a smaller wrench. or vice grips. I haven't had much luck with the nut breakers, but I know people who have. Grinders are usually easier to cut off nuts with than the hack saw is. Finally, Sears makes a set of tools for removing rounded nuts / bolts. They work basically like screw extractors, but they fit over the rounded head instead of going into a drilled hole. I have had some luck with them in the past.
You would have saved yourself a lot of work by dealing with that nut instead of cutting the ball joint apart. You CAN NOT use the pickle fork to remove the joint until that nut has been taken off! Once the nut is off (either by unscrewing it, or by cutting / grinding it) then the pickle fork will pop the joint out with just a few good whacks.
#8
hmm... okay
well this isnt going good
I got the spindle nut off, by grinding new wrench grips into it. but for the life of me cant get the threaded bolt to pop out.
http://i5.photobucket.com/albums/y15...4/92max/1a.jpg
http://i5.photobucket.com/albums/y15...4/92max/2b.jpg
Im not sure how a hammer is gonna fit in there unless i use the claw part.
(and i'm not keen on removing the axle)
I've broken two screwdrivers by putting them in the hole for the bolt clip and trying to turn it to get leverage. (while using a blow torch)
Also, If this (below) is the tie rod end, i'm definitely going to need an aligment. Is there a way to tighten it?
http://i5.photobucket.com/albums/y15...MAGE_00037.jpg
And thank you Tquick.. I totally misinterpreted the instructions in the howto.. I see it would have been craploads easier to loosen the top bolt first.

I got the spindle nut off, by grinding new wrench grips into it. but for the life of me cant get the threaded bolt to pop out.
http://i5.photobucket.com/albums/y15...4/92max/1a.jpg
http://i5.photobucket.com/albums/y15...4/92max/2b.jpg
Im not sure how a hammer is gonna fit in there unless i use the claw part.
(and i'm not keen on removing the axle)
I've broken two screwdrivers by putting them in the hole for the bolt clip and trying to turn it to get leverage. (while using a blow torch)
Also, If this (below) is the tie rod end, i'm definitely going to need an aligment. Is there a way to tighten it?
http://i5.photobucket.com/albums/y15...MAGE_00037.jpg
And thank you Tquick.. I totally misinterpreted the instructions in the howto.. I see it would have been craploads easier to loosen the top bolt first.
Last edited by smitty124; 11-26-2007 at 09:32 AM.
#9
welp...here's the problem..you cut off the bottom part so you don't have a leverage point to pry down anymore. i did this once and learned my lesson.
well you don't want to totally remove the axle..you just want to slide it out of the spindle. your call..you can work on the ball joint stud and pray that it will go out or remove the axle nut pull the spindle out and then take a big hammer and hit that ball joint stud down.
if you're really not looking to move the axle then may i suggest drilling a hole from the bottom into the balljoint stud and see if that weakens it enough for you to push it down.
yes that's the tie rod...if that's loose to the point where there's a lot of play then get a new tie rod.
well you don't want to totally remove the axle..you just want to slide it out of the spindle. your call..you can work on the ball joint stud and pray that it will go out or remove the axle nut pull the spindle out and then take a big hammer and hit that ball joint stud down.
if you're really not looking to move the axle then may i suggest drilling a hole from the bottom into the balljoint stud and see if that weakens it enough for you to push it down.
yes that's the tie rod...if that's loose to the point where there's a lot of play then get a new tie rod.
#10
mmk, i got it out by torching the top for 5 mins, then spraying cleaner on it, to quickly cool it, then got it out with hammer and chisel..
How much is a tie rod, and how hard is the repair? Is there any way I can just put it back together, and make it to toronto this aft, and i'll drop it off for an aligment tomorrow morning..
eg can I put it back together and drive it safely for about 70 km?
How much is a tie rod, and how hard is the repair? Is there any way I can just put it back together, and make it to toronto this aft, and i'll drop it off for an aligment tomorrow morning..
eg can I put it back together and drive it safely for about 70 km?
#11
wooo nice...congrats on getting it out.
tie rods...i think like 40 bucks. w/ the right tools it's not hard but you MUST get an alignment afterwards.
depends on how loose it is...you can go for a little while but it's really loose get it fixed ASAP.
tie rods...i think like 40 bucks. w/ the right tools it's not hard but you MUST get an alignment afterwards.
depends on how loose it is...you can go for a little while but it's really loose get it fixed ASAP.
#12
what Danno said.
ball joints and tie rod ends are about $35 each from the parts store. you will definitely need an alginment afterwards, but if you count the threads/turns it takes to separate the inner/outer tie rods, then you can get it pretty close and can drive 70km without eating too much tire. get the alignment done ASAP though.
and if you're replacing these only on one side, go ahead and do the other side as well. if one's bad, the other is never far behind.
ball joints and tie rod ends are about $35 each from the parts store. you will definitely need an alginment afterwards, but if you count the threads/turns it takes to separate the inner/outer tie rods, then you can get it pretty close and can drive 70km without eating too much tire. get the alignment done ASAP though.
and if you're replacing these only on one side, go ahead and do the other side as well. if one's bad, the other is never far behind.
#13

#14
The ball joint is a taper fit. Which means as you tighten the 22mm nut you pull the taper tighter as well. I would say your best bet now is to cut the nut off so you can force the taper back down thru the steering knuckle.
#16
Dude, you should do you tierods while its all apart, now that you got a torch it should be no problem. Another thing you can do is not remove the old nut thats beside the tierod and when yput put in the new one it should stop turning when it gets to that nut therefore your aligment should be the same UNLESS the tierod is a different size.
I spent 35 bucks on each TRW tierod with lifetime warranty but I've heard OEM/
Moog is a lot better...
Oh and just so you see the importance of a tierod, if it breaks; your wheel will have no control and will cause a big accident especially if you're doing long distance driving
I spent 35 bucks on each TRW tierod with lifetime warranty but I've heard OEM/
Moog is a lot better...
Oh and just so you see the importance of a tierod, if it breaks; your wheel will have no control and will cause a big accident especially if you're doing long distance driving
#17
When I do tie rod ends, I break the jamb nut loose, just barely, perhaps between 1/8 and 1/4 turn, then wrap some electrical tape around the rod so that the edge of the electrical tape is just touching the nut. I then remove the rod end, and the old nut, and thread the new nut on, carefully until it just touches the edge of the electrical tape. Next I thread on the rod end until it just touches the nut, and then turn it back just enough so that it is in the correct plane to line up with the hole in the steering knuckle. Finally, I tighten the jamb nut, which should only need 1/8 to 1/4 turn to tighten. As long as the new tie rod, and the old one are the same size, this will get your alignment pretty close to where it was before. You'll still need to get aligned as soon as you can, but it should be safe to drive that way.
#18
Here's another way around this issue for whenever it happens again. NO CUTTING NECESSARY.
Support car with jack stands,put jack under ball joint and lift. The pressure will hold the nut from spinning when you try to loosen it.
You can also do it the other way; put jackstands under ball joint while car is supported by jack. (other option is safer though)
Do this and voila! your ball joint is out!
Support car with jack stands,put jack under ball joint and lift. The pressure will hold the nut from spinning when you try to loosen it.
You can also do it the other way; put jackstands under ball joint while car is supported by jack. (other option is safer though)
Do this and voila! your ball joint is out!
#19
well here's the thing...you can support the weight on the ball joint but you're going to work harder to get it out of the spindle.
if it's spinning while you're turning then it's loose enough for you to get it out.
if it's really rusted in there, you don't need to use the jack/stand hold it..it's already crazy tight.
if it's spinning while you're turning then it's loose enough for you to get it out.
if it's really rusted in there, you don't need to use the jack/stand hold it..it's already crazy tight.
#20
well here's the thing...you can support the weight on the ball joint but you're going to work harder to get it out of the spindle.
if it's spinning while you're turning then it's loose enough for you to get it out.
if it's really rusted in there, you don't need to use the jack/stand hold it..it's already crazy tight.
if it's spinning while you're turning then it's loose enough for you to get it out.
if it's really rusted in there, you don't need to use the jack/stand hold it..it's already crazy tight.
You're thinking of it the other way...I'm referring to what happened to the OP.
If when you try to loosen the 22mm nut on top the whole ball is spinning, then you have to apply pressure so you can actually loosen the nut.
You're thinking of it already being cut and loose right?
#21
You're thinking of it the other way...I'm referring to what happened to the OP.
If when you try to loosen the 22mm nut on top the whole ball is spinning, then you have to apply pressure so you can actually loosen the nut.
You're thinking of it already being cut and loose right?
If when you try to loosen the 22mm nut on top the whole ball is spinning, then you have to apply pressure so you can actually loosen the nut.
You're thinking of it already being cut and loose right?
it is loose in the spindle where you need a jack below it to put pressure on it then we can both agree that once the bolt is out it's not going to take too much to pop out the ball joint shaft right (compared to being rusted in the spindle).
from what the OP posted it looked like the ball joint shaft was rusted/frozen into the spindle...hence there's no need for the jack under the ball joint since the damn ball joint shaft is already rusted solid on the spindle.
got it?
#23
The problem wasn't that the tapered bolt was spinning with the nut, the problem was that he misread the instructions for removing the thing, and tried to pickle fork it out without removing the nut first, so all he did was mangle the hell out of the ball joint. What was loose was the ball socket on the ball, not the tapered bolt in the control arm hole. He then cut off the joint part, leaving the tapered bolt still in the control arm, with the nut still on it, and still tight. Then, after getting the nut off, he had to figure out how to get the tapered bolt out, since he no longer had a ball joint to use the pickle fork on.
What you are saying about using the jack to put pressure on the joint in order to hold the tapered bolt still will work, but if the tapered bolt is loose enough to spin when you turn the nut, why not just cut the nut off, and watch the ball joint just fall out of the control arm, instead of using the jack to ram it back in, then unscrewing the nut, then having to use the pickle fork again to break it loose.
What you are saying about using the jack to put pressure on the joint in order to hold the tapered bolt still will work, but if the tapered bolt is loose enough to spin when you turn the nut, why not just cut the nut off, and watch the ball joint just fall out of the control arm, instead of using the jack to ram it back in, then unscrewing the nut, then having to use the pickle fork again to break it loose.
Thread
Thread Starter
Forum
Replies
Last Post
soon2ownmax
6th Generation Maxima (2004-2008)
0
08-13-2015 02:19 PM