Hybrid Q
#1
Guest
Posts: n/a
Hybrid Q
I'm thinking of messing with VTC's and making some thing to control them. But I want to use the 3L heads with my setup. But since people use the non VTC timing chain covers on VTC engines I'm assuming its possible to swap VTC's on a non VTC engine Correct?.
My setup:
3L
crank & rods
heads
modified USIM (ITB's)
3.5L
pistons
block
VTC's/cover
And dont bash my setup, I just need to know if vtc's are possible
~Alex
My setup:
3L
crank & rods
heads
modified USIM (ITB's)
3.5L
pistons
block
VTC's/cover
And dont bash my setup, I just need to know if vtc's are possible
~Alex
#3
Yes it is possible to swap VTC onto a non-VTC engine by changing the heads and timing equipment. The Pathfinder is the perfect example given the fact that it is actually our engine with VTC, but the problem is that you need an ECU to control it. No piggyback including EU can control VTC. A standalone will do it, but you are talking a lot of work without a lot of reward. It would be easier to use a full 3.5 setup in my opinion over trying to make this hybrid work.
#5
Originally Posted by NmexMAX

However, with the release of the v-manage, hopefully in March, a whole new area of VTC tuning will open up for those of us that are "VTC ready".
#6
Guest
Posts: n/a
I figured the 3.5 heads were drilled/casted with oil gallies (sp?). I just wasn't sure.
One more advantage for the 3.5L heads....
As for controlling them, I'm talking to a guy about a simple version of megasquirt just for VTC's. Then we could set it up to control most types of cam timing/lift systems. But thats a long way off.
ENG92- YGPM
~Alex
One more advantage for the 3.5L heads....
As for controlling them, I'm talking to a guy about a simple version of megasquirt just for VTC's. Then we could set it up to control most types of cam timing/lift systems. But thats a long way off.
ENG92- YGPM
~Alex
#7
Originally Posted by Alex_V
ENG92- YGPM
~Alex

Originally Posted by Alex_V
As for controlling them, I'm talking to a guy about a simple version of megasquirt just for VTC's. Then we could set it up to control most types of cam timing/lift systems. But thats a long way off.
~Alex
~Alex
Once you hit open loop, all the other "tunable" systems (ie fuel, timing) resort to lookup tables based on engine load and rpm. However, the VTC phasers still have to constantly make angle corrections based on feedback from the crank and cam sensors.
The stock VQ35 crank and cam signal waveforms are significantly more complicated than those of the VQ30. But they need to be that way in order to track a cam that can have its own degree of freedom relative to the crank.
If and when the time comes, I can provide you with crank and cam signal waveforms if required.
#10
Originally Posted by krismax
I have posted this before but i have a SCC issue where JWT made VTC work with just using a nitrous control module
There were only 2 cam positions on those engines. No feedback is required.
The control signal to the solenoid is either 0V or battery voltage? You could control that with an RPM switch.
#11
Aren't the new Nissan VTCs pretty dynamic? They aren't just a on/off thing like the old VTCs in the VE30DE. Even these old ones operated off/on/off thoughout the rpm range. I suppose you "could" control them like an on/off deal aka MEVI but I don't think you will be getting same type of gains. I would think one would need mapping capabilities on the order of a a/f graph
#12
Ok guys found it its a s14 silvia motor(SR20) with VTC.here it reads
The greatest swap challenge was still ahead."We were able to perform the mechanical conversion,but the Datsun engineers who designed the 1967 electrical system couldn't have imagined it would ever need to run Variable Timing Control." Thankfully, Jim Wolf Technology supplied a first-generation 240SX ECU to provide spark and fuel mapping. Controlling the VTC would call for a very unique application of a JWT product.
The roadster lacked a modern speed sensor to trigger the VTC,so Clark Steppler of JWT looked to the company's Nitrous Control Module to engineer around the input signals normally recieved to activate the VTC. The first major change was to wire the Nitrous Module to accept a signal feed for RPM rather than vehicle speed. Then the module's output was tweaked into activating the VTC . Genius.
Throttle position and water temperature were then routed through the JWT Nitrous Module . With all three feeds sent to the 240 SX ECU, it now controls the variable timing engine as if VTC had always dwelled beneath the hood of this roadster.
The greatest swap challenge was still ahead."We were able to perform the mechanical conversion,but the Datsun engineers who designed the 1967 electrical system couldn't have imagined it would ever need to run Variable Timing Control." Thankfully, Jim Wolf Technology supplied a first-generation 240SX ECU to provide spark and fuel mapping. Controlling the VTC would call for a very unique application of a JWT product.
The roadster lacked a modern speed sensor to trigger the VTC,so Clark Steppler of JWT looked to the company's Nitrous Control Module to engineer around the input signals normally recieved to activate the VTC. The first major change was to wire the Nitrous Module to accept a signal feed for RPM rather than vehicle speed. Then the module's output was tweaked into activating the VTC . Genius.
Throttle position and water temperature were then routed through the JWT Nitrous Module . With all three feeds sent to the 240 SX ECU, it now controls the variable timing engine as if VTC had always dwelled beneath the hood of this roadster.
#14
Originally Posted by Jeff92se
Yes but aren't the VQ35 VTCs continusly varible? Not just on/off like the SR20 units?
theres somebody right now working on VTC's on a VQ30

#15
Originally Posted by Jeff92se
Yes but aren't the VQ35 VTCs continusly varible? Not just on/off like the SR20 units?
http://forums.maxima.org/showpost.ph...1&postcount=50
#17
The most important difference like eng92 has said over and over again is that the CVTC system in particular needs FEEDBACK CONTROL throughout it's operation. There needs to be something controlling it that constantly knows the cam position. And like you said Jeff, it's continuously variable and controls the sprocket by constantly changing the pulse width sent to the solenoid and balancing it against the parasitic drag that the cam experiences to precisely locate the cam angle.
#19
Originally Posted by 95naSTA
So, the VCT solenoid(s?) is/are pulse width modulated like an injector?
Couldn't you use a stamp micro computer?
People often use these to control another injector.
Couldn't you use a stamp micro computer?
People often use these to control another injector.
Originally Posted by nismology
The most important difference like eng92 has said over and over again is that the CVTC system in particular needs FEEDBACK CONTROL throughout it's operation. There needs to be something controlling it that constantly knows the cam position.
#20
Originally Posted by nismology
Driving an injector doesn't require feedback control.
j/k Mike, I thought I would throw that in for comic relief.

#21
Originally Posted by nismology
Driving an injector doesn't require feedback control.
Driving one with a stamp does require inputs, maps, and a formula which is what the VCTs would need. You could correlate a pulse width with advance/retard and monitor the pulse width.
#22
Originally Posted by 95naSTA
Yeah... I read that.
Driving one with a stamp does require inputs, maps, and a formula which is what the VCTs would need. You could correlate a pulse width with advance/retard and monitor the pulse width.
Driving one with a stamp does require inputs, maps, and a formula which is what the VCTs would need. You could correlate a pulse width with advance/retard and monitor the pulse width.
#23
A microcomputer like the BASIC STAMP series is a viable option for independent VTC control. However it is not for the faint of heart and is probably beyond the means, technically, of most of the people on here.
You are essentially building your own controller from a collection of pc boards which you have to interface together. After you have the necessary hardware assembled, you need to write the software to make it all work.
Even if you have the technical ability to do that, you still need to have “appropriate” signal inputs to find your actual cam position.
This applies to VQ35 swaps using the VQ30 ecu. The crank position is easy. You can use the existing VQ30 crank REF and POS sensors for that. You will need to rig a mounting on the timing cover for the crank REF sensor.
Now that you have the VQ35 timing covers back on to accommodate the VTC phasers, you no longer have a 3.0 cam sensor. You can output a pulse signal from the STAMP to keep the ecu happy.
The two stock VQ35 cam sensors can be wired into the controller for the all important cam positon signals.
One thing that may be a cause of concern is that the VQ30 ecu might get upset if the cam position signal it sees is varying in relation to the crank signal. Of course, if you are using a controller generated signal you can always just fix it based on rpm.
It would be an interesting project with plenty of learning value.
You are essentially building your own controller from a collection of pc boards which you have to interface together. After you have the necessary hardware assembled, you need to write the software to make it all work.
Even if you have the technical ability to do that, you still need to have “appropriate” signal inputs to find your actual cam position.
This applies to VQ35 swaps using the VQ30 ecu. The crank position is easy. You can use the existing VQ30 crank REF and POS sensors for that. You will need to rig a mounting on the timing cover for the crank REF sensor.
Now that you have the VQ35 timing covers back on to accommodate the VTC phasers, you no longer have a 3.0 cam sensor. You can output a pulse signal from the STAMP to keep the ecu happy.
The two stock VQ35 cam sensors can be wired into the controller for the all important cam positon signals.
One thing that may be a cause of concern is that the VQ30 ecu might get upset if the cam position signal it sees is varying in relation to the crank signal. Of course, if you are using a controller generated signal you can always just fix it based on rpm.
It would be an interesting project with plenty of learning value.
#24
Guest
Posts: n/a
ENG92- I'll pm you later today when I have Betton's email.
Now megasquirt is a very simple ECU and only needs one crank sensor most of the time.
Knowing that I came up with the idea of a simple controller, but all it would need is the output to control the VTC and 2 inputs,3 max, then have a map just like injectors or ignition. Because with VTC's you can just tune them, you don't need to know when the engine is hot only when the rpm's are at, and TPS.
Of course this is for standalone setups I'm not sure if this would work for the 3.5 with 3L ecu. But if you could just put a cam sensor in the front of the timing cover (driven at the correct speed) it wouldn't matter what your doing to your cams for all the ECU cares. Or if you have intake only VTC and the cam sensor is on the exhaust it also doesn't matter.
~Alex
Now megasquirt is a very simple ECU and only needs one crank sensor most of the time.
Knowing that I came up with the idea of a simple controller, but all it would need is the output to control the VTC and 2 inputs,3 max, then have a map just like injectors or ignition. Because with VTC's you can just tune them, you don't need to know when the engine is hot only when the rpm's are at, and TPS.
Of course this is for standalone setups I'm not sure if this would work for the 3.5 with 3L ecu. But if you could just put a cam sensor in the front of the timing cover (driven at the correct speed) it wouldn't matter what your doing to your cams for all the ECU cares. Or if you have intake only VTC and the cam sensor is on the exhaust it also doesn't matter.
~Alex
#25
Originally Posted by Alex_V
Now megasquirt is a very simple ECU and only needs one crank sensor most of the time.
Knowing that I came up with the idea of a simple controller, but all it would need is the output to control the VTC and 2 inputs,3 max, then have a map just like injectors or ignition. Because with VTC's you can just tune them, you don't need to know when the engine is hot only when the rpm's are at, and TPS.
Knowing that I came up with the idea of a simple controller, but all it would need is the output to control the VTC and 2 inputs,3 max, then have a map just like injectors or ignition. Because with VTC's you can just tune them, you don't need to know when the engine is hot only when the rpm's are at, and TPS.
The key to understanding this is: There is no correlation whatsoever between the width of the pulse signal sent to the VTC solenoid and the cam position. Rate of position change - YES, absolute position - NO
Maps for injectors are a matrix of fixed values (in ms) for which you want the injectors to open for.
You do not know what the solenoid pulse width is ahead of time so there is no map to be made. Pulse width is determined in realtime by observing the deviation between where the cam is and where the map calls for it to be.
My apologies Alex if this is already very obvious to you, but it wasn't clear to me in your post if that was the case.
#26
Using Megasquirt
Hey guys. I'm one of the proponents for using MS to control VTC's. Good to see a thread with some technical input on VQ35 VTC operation!
Eng92, please correct me if I'm misunderstanding something.
Quoting the FSM:
(FSM>>Engine>>Engine Control System>>IVT Control Solenoid [pg 404]
My understanding of that excerpt is that the required variable for VTC control is the duration (Pulse Width duration, same as injector duration).
My understanding of what You (Eng92) were saying is that the duration is locked in (i.e. the injector maps would have a constant value across the enntire closed loop range, and go to another lookup value in open loop) and that the relative timing of this event (relative to cam position) is what needs to be varied, not the duration.
Please confirm or explain.
Also, I'm still not convinced that the cam sensor does anything more than indirectly measure timing belt/chain stretch... (i.e. u can get cam position from the crank using the pulley ratio of the two). Please educate me.
Thanks for Your time.
Regards,
H. Kurt Betton
Eng92, please correct me if I'm misunderstanding something.
Quoting the FSM:
Intake valve timing control solenoid valve is activated by ON/OFF
pulse duty (ratio) signals from the ECM.
The intake valve timing control solenoid valve changes the oil
amount and direction of flow through intake valve timing control unit
or stops oil flow.
The longer pulse width advances valve angle.
The shorter pulse width retards valve angle.
When ON and OFF pulse widths become equal, the solenoid valve
stops oil pressure flow to fix the intake valve angle at the control
position.
pulse duty (ratio) signals from the ECM.
The intake valve timing control solenoid valve changes the oil
amount and direction of flow through intake valve timing control unit
or stops oil flow.
The longer pulse width advances valve angle.
The shorter pulse width retards valve angle.
When ON and OFF pulse widths become equal, the solenoid valve
stops oil pressure flow to fix the intake valve angle at the control
position.
My understanding of that excerpt is that the required variable for VTC control is the duration (Pulse Width duration, same as injector duration).
My understanding of what You (Eng92) were saying is that the duration is locked in (i.e. the injector maps would have a constant value across the enntire closed loop range, and go to another lookup value in open loop) and that the relative timing of this event (relative to cam position) is what needs to be varied, not the duration.
Please confirm or explain.
Also, I'm still not convinced that the cam sensor does anything more than indirectly measure timing belt/chain stretch... (i.e. u can get cam position from the crank using the pulley ratio of the two). Please educate me.
Thanks for Your time.
Regards,
H. Kurt Betton
#27
Linking my original proposal to this one incase anybody wants an overview:
http://www.engineswaptech.com/forums...read.aspx#1686
http://www.engineswaptech.com/forums...read.aspx#1686
#28
Originally Posted by bettonracing
My understanding of that excerpt is that the required variable for VTC control is the duration (Pulse Width duration, same as injector duration).
Yes that is correct. That is how you control the solenoids.
But you do not know what the duration needs to be ahead of time. It is not a function of rpm or load. It is a function of how much the cams current position differs in advance or retard of where it is supposed to be.
(For example: if at the current rpm and load, the cam sensor says the cam is currently 15 degrees advanced and the map calls for 17 degrees advanced, the solenoid duty cycle will increase above 40% briefly to advance the cam to 17 degrees. When the cam sensor reads it at 17 degrees, the solenoid duty cycle will return to 40%.)
This is illustrated nicely in the graph below which shows the effect of duty cycle on the advance and retard of the cam angle.
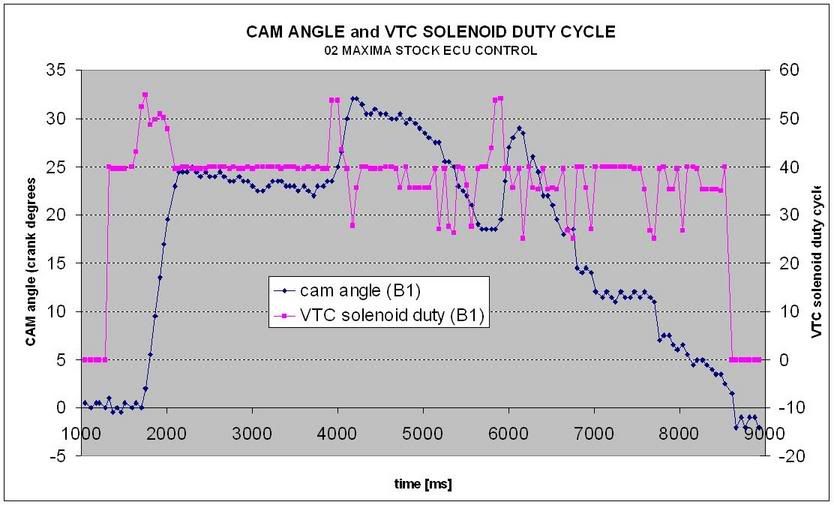
Originally Posted by bettonracing
My understanding of what You (Eng92) were saying is that the duration is locked in (i.e. the injector maps would have a constant value across the enntire closed loop range, and go to another lookup value in open loop) and that the relative timing of this event (relative to cam position) is what needs to be varied, not the duration.
Please confirm or explain.
Please confirm or explain.
Think of it this way. The cam sensor is analagous to your O2 sensor. In closed loop fuel control, the ecu reads the O2 sensor and trims your fuel either +/- to try and keep the mixture stoich. Same thing with the VTCs except now instead of a constant A/F of 14.7, the desired cam angle is a function of both rpm and load. (That is your map) Now you adjust the solenoid duty cycle to "trim" the cam position advance/retard to get it to follow the map as closely as possible.
#29
On my 350z race car I want to change out to the VQ35 and would like to use the variable cams. The car is running a Motec and picks a signal from the VQ30 cam sensor on the timing cover.I was comparing the VQ30 to VQ35 heads and noticed that the cams have a sensor at the back of the cam. I pulled the cam sensor out of the VQ30 and stuck it in the VQ35 head and it will fit and it is short enough that I think I can fabricate an adapter for the back of the cam to get the signal to the sensor and not have to use the VQ30 timing cover.
#30
Originally Posted by eng92
(For example: if at the current rpm and load, the cam sensor says the cam is currently 15 degrees advanced and the map calls for 17 degrees advanced, the solenoid duty cycle will increase above 40% briefly to advance the cam to 17 degrees. When the cam sensor reads it at 17 degrees, the solenoid duty cycle will return to 40%.)
Think of it this way. The cam sensor is analagous to your O2 sensor. In closed loop fuel control, the ecu reads the O2 sensor and trims your fuel either +/- to try and keep the mixture stoich. Same thing with the VTCs except now instead of a constant A/F of 14.7, the desired cam angle is a function of both rpm and load. (That is your map) Now you adjust the solenoid duty cycle to "trim" the cam position advance/retard to get it to follow the map as closely as possible.
Think of it this way. The cam sensor is analagous to your O2 sensor. In closed loop fuel control, the ecu reads the O2 sensor and trims your fuel either +/- to try and keep the mixture stoich. Same thing with the VTCs except now instead of a constant A/F of 14.7, the desired cam angle is a function of both rpm and load. (That is your map) Now you adjust the solenoid duty cycle to "trim" the cam position advance/retard to get it to follow the map as closely as possible.
#31
All comes back to feedback control. 
Also, doesn't something like oil pressure affect how much the cam angle needs to be trimmed due to increased/decreased oil flow to the solenoid and drag on the cam varying ever-so-slightly?

Also, doesn't something like oil pressure affect how much the cam angle needs to be trimmed due to increased/decreased oil flow to the solenoid and drag on the cam varying ever-so-slightly?
#33
Originally Posted by nismology
All comes back to feedback control. 
Also, doesn't something like oil pressure affect how much the cam angle needs to be trimmed due to increased/decreased oil flow to the solenoid and drag on the cam varying ever-so-slightly?

Also, doesn't something like oil pressure affect how much the cam angle needs to be trimmed due to increased/decreased oil flow to the solenoid and drag on the cam varying ever-so-slightly?
Of course there is a tolerance that will allow small deviations in cam position to occur before action is taken. This can be seen in the previous graph where there is no change in the solenoid duty cycle for about 2 seconds but the cam angle slowly retards by almost 3 degrees.
#34
Aha! It makes perfect sense now. I need to absorb some more information and take another stab.
Initial thots indicate some [relatively mild] circuitry and software adjustments still make it feasible w/ the MS2. But lemme get up to date first.
Regards,
H. Kurt Betton
Initial thots indicate some [relatively mild] circuitry and software adjustments still make it feasible w/ the MS2. But lemme get up to date first.
Regards,
H. Kurt Betton
#35
Originally Posted by eng92
Any cam deviations as a result of external force influences (such as drag on the cam) or changes in vtc phaser adjustment rates (due to oil pressure) are automatically handled because there is a feedback control system.
I was just giving another concrete reason why feedback control is required.

#36
Originally Posted by bettonracing
Also, I'm still not convinced that the cam sensor does anything more than indirectly measure timing belt/chain stretch... (i.e. u can get cam position from the crank using the pulley ratio of the two). Please educate me.
Thanks for Your time.
Regards,
H. Kurt Betton
Thanks for Your time.
Regards,
H. Kurt Betton
With VTCs, the cam position is no longer a simple function of crank position. It can be varied up to 40 crank-angle degrees (in the case of the VQ35) Therefore the cam sensors are necessary to determine where in that 40 degree range the cam actually is.
No cam sensor?? That is almost "old" school. I guess that means you are running simultaneous fuel injection with a wasted spark ignition system.
#37
Originally Posted by nismology
Exactly!
I was just giving another concrete reason why feedback control is required.
I was just giving another concrete reason why feedback control is required.

I did not realize your question was rhetorical. I should know by now that you know most of this stuff already.
#38
Originally Posted by eng92
With VTCs, the cam position is no longer a simple function of crank position. It can be varied up to 40 crank-angle degrees (in the case of the VQ35) Therefore the cam sensors are necessary to determine where in that 40 degree range the cam actually is.
Originally Posted by eng92
No cam sensor?? That is almost "old" school. I guess that means you are running simultaneous fuel injection with a wasted spark ignition system.
Actually yes I am! Until I can justify the cost effectiveness of sequential fuel & spark capable ecu for my applications (which range from street to race), I see absolutely no need for it.
Regards,
H. Kurt Betton
Thread
Thread Starter
Forum
Replies
Last Post
umnitza
Group Deals / Sponsors Forum
0
09-01-2015 01:03 PM
micahdc
General Maxima Discussion
7
05-27-2002 07:06 AM
speedtrip
4th Generation Maxima (1995-1999)
43
05-20-2002 03:26 PM
Capitone
4th Generation Maxima (1995-1999)
9
04-11-2001 08:16 AM